Shagang 4# blast furnace was repaired using the overall pouring technology of the furnace cylinder developed by Huaxi Technology, and then the furnace was shut down in 2022 due to capacity policy requirements. Shagang Group made an analysis report on the 4# blast furnace medium repair project.
Brief introduction and furnace type parameters of 4# blast furnace in 1. Shagang
Shagang 4# blast furnace was put into operation on February 28, 2013. The blast furnace was in good condition for two years at the beginning of operation, and there was no material collapse and suspension throughout the year.
Starting from 2016, due to the large use of high-zinc materials, the zinc load will reach up to 1.8 ㎏/t, coupled with long-term use of water coke quenching, insufficient blast furnace top temperature and poor zinc discharge capacity, resulting in serious blast furnace thickness, destruction of blast furnace furnace furnace type, and forced strong development edge of blast furnace. Due to the increase of molten iron circulation, furnace cylinder erosion will intensify, furnace cylinder temperature will rise obviously, and local water temperature difference will reach 0.7 ℃, the heat flow intensity reached 12785.3Kcal/m2.h, and the furnace skin temperature reached 55°C. The blast furnace has taken measures such as adding vanadium titanium ore, reducing the area of the tuyere, controlling the metallurgical strength, blocking the tuyere and so on.
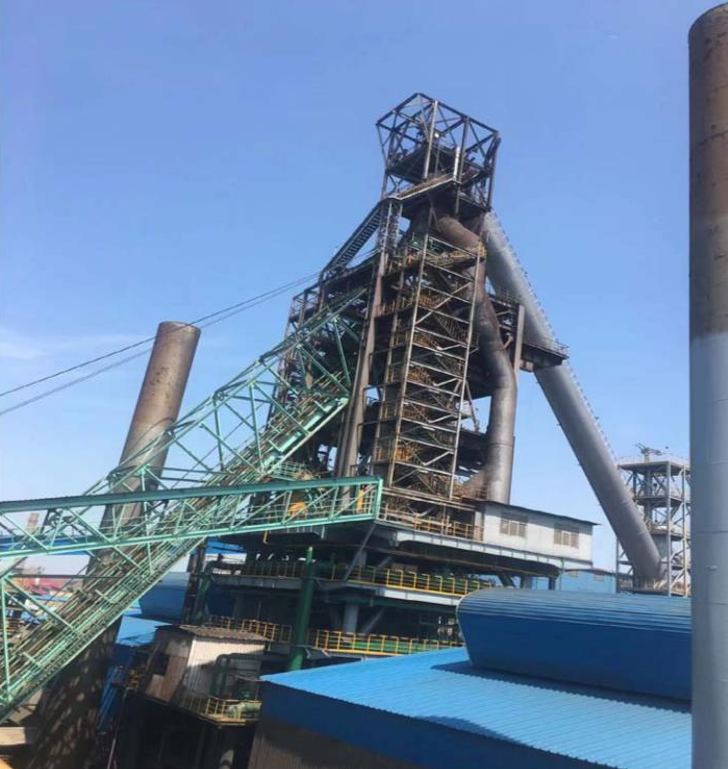
According to industry statistics,Integral Casting Technology of Huaxi Furnace CylinderIt has become the first choice for rapid repair of blast furnaces. Shagang has done its part in the application of new technologies and is brave to be the vanguard of scientific and technological innovation in the new era. In 2019, furnace 4 will be poured into the furnace cylinder, which will be undertaken by Henan Huaxi Science and Technology Group. Due to policy needs, the furnace was shut down after 2 years and 4 months of use. After on-site measurement, the furnace cylinder erosion was in good condition and exceeded the expected target.
Integral Casting Technology of Huaxi Furnace CylinderThe seamless combination of the pouring ceramic cup and the carbon brick makes the furnace structure closer; there is no filling layer between the traditional ceramic cup and the carbon brick, which reduces the thermal resistance, ensures the overall heat transfer efficiency of the pouring furnace, achieves the heat transfer balance, protects the furnace lining safety and avoids the occurrence of hidden dangers. The thickness of the pouring furnace is close to the thickness of the original ceramic cup.
Temperature trend of 2. hearth before pouring
Before the mid-repair in November 2019, the furnace temperature elevation is 7.64m, the TE6107-4A5 galvanic insertion depth is 250mm, the maximum temperature is 760 ℃, the water temperature difference is 0.7 ℃, and the thermal intensity is 12785.3Kcal/m2.h.
Evaluation of 3. Furnace Cast and Erosion State
1. Erosion state before medium repair
Judging from the situation of the grill furnace, the erosion of the blast furnace is relatively serious and irregular, mainly because the erosion at the entrance of the two inlet pipes at the bottom of the blast furnace is very serious. As shown in the figure, the erosion of the foot area of the 7 layers is the most serious, below the 14#-15# tuyere due north and below the 6#-7# tuyere due south. The residual amount of carbon brick at the corresponding position of 6#-7# tuyere is at least 20mm, and the residual amount of carbon brick at the corresponding position of 14#-15# tuyere is at least 25mm. According to the erosion model drawn according to the field measurement data:
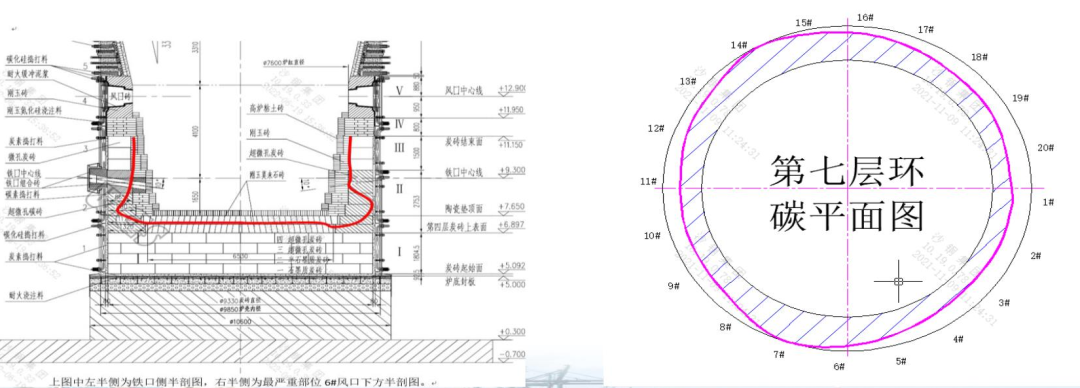
2. Evaluation of furnace cylinder pouring and later erosion state
The construction period of furnace cylinder pouring is from November 7 to December 8, 2019, which lasts for 30 days, including 15 days for cleaning the furnace with residual iron, 5 days for pouring, 2 days for spraying, 2 days for other work and 6 days for drying.
The specific furnace cylinder pouring scheme is finally determined as follows after full discussion between Huaxi science and technology engineering experts and Shagang engineers:
■ The tuyere belt, hearth bottom and repaired carbon brick parts are designed with tuyere belt castable, hearth castable and high thermal conductivity castable respectively.
■ Pouring is carried out in 6 sections. The thickness of the two layers at the bottom of the furnace is 800mm, the thickness of the side wall above the slag door is 350mm, and the thickness of the side wall of the slag door is 700mm. The blast furnace lining is formed as shown in the right figure: (details of specific pouring are omitted)
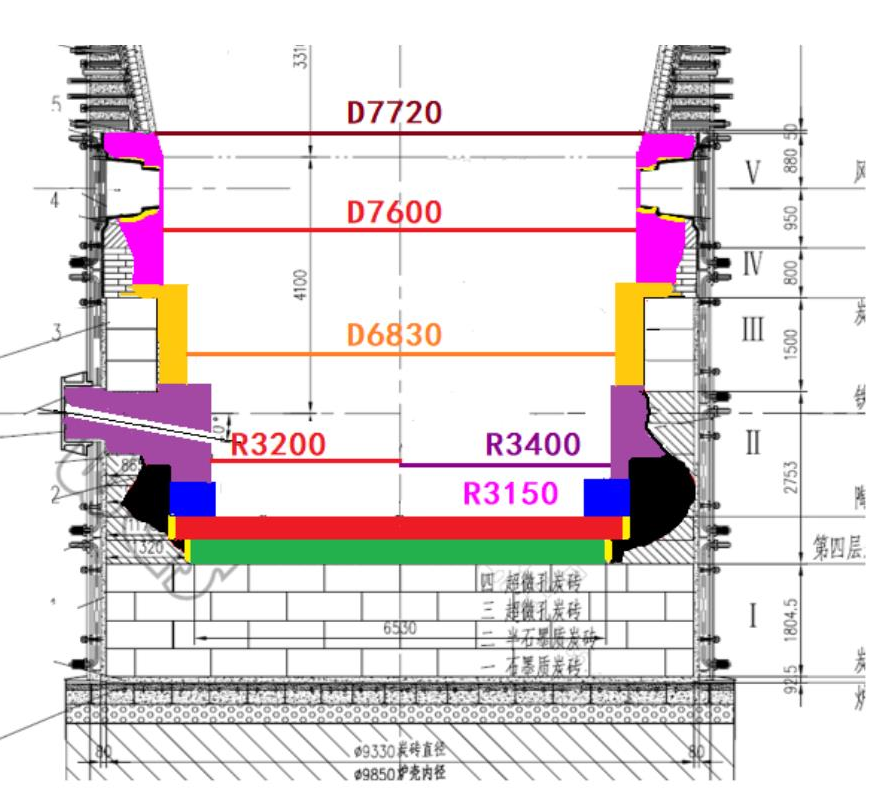
Brief Analysis on Production of 4. Hearth after Pouring
After the blast furnace is poured, the water temperature difference in the furnace cylinder enters a relatively well controlled state, which is stable at about 0.3 ℃ for a long time, the heat flow intensity is below 5000 Kcal/㎡.h, and the temperature of the slag gate is also generally good. Due to the safe control of the furnace body and the good recovery of the furnace type, the use level of oxygen enrichment in blast furnace air volume has been greatly improved, the production index has reached the best level in history, the fuel ratio is 520 ㎏, and the highest monthly average daily production is close to 4000 tons.
Changes in cooling mode of blast furnace: after considering the demolition of multiple blast furnaces, it is found that the bottom erosion is very little, more of which is the furnace cylinder ring carbon, like the foot area, so the cooling water amount of the furnace bottom is appropriately reduced from 350m/hour to 300m/hour, in order to expect the formation of bottom erosion, thus slowing down the side wall erosion of the furnace cylinder.
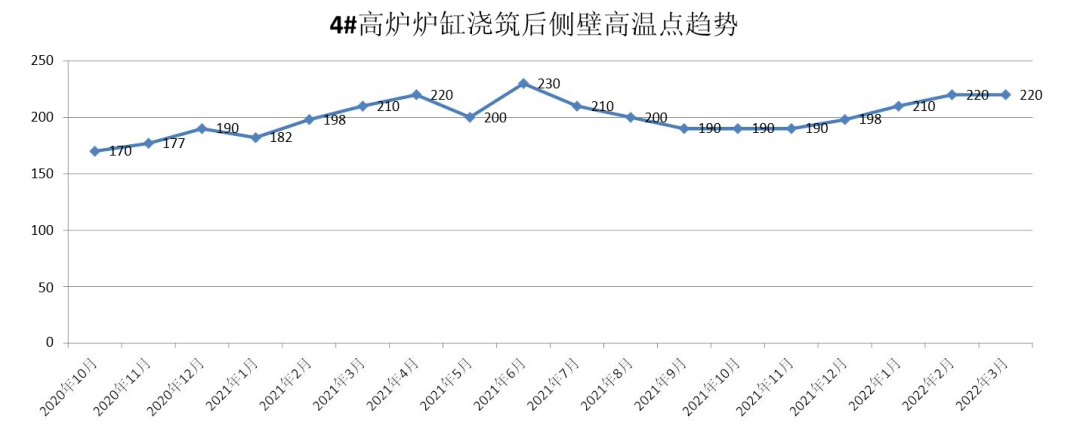
After the furnace cylinder is poured and produced, until the furnace is shut down in March 2022, the temperature of the furnace cylinder is relatively stable as a whole, with the highest elevation of 7.64m, the TE6107-4A5 galvanic temperature has been stable within 250 ℃, the water temperature difference is up to 0.2 ℃, and the thermal strength is below 5000K cal/m2 * h, which is classified according to the control level of the furnace body management system of the ironmaking plant and belongs to the safe range.
Investigation on erosion of castable after shutdown of 5. furnace
By March 26, 2022, due to the demand of production capacity policy, the No. 4 furnace will be shut down for 2 years and 4 months after medium repair. Because it is a destructive demolition method, it is more difficult to restore the overall erosion state. However, the overall water temperature difference and the temperature of each layer are relatively normal before shutdown. Combined with the residual refractory of each part removed, the analysis and inference are as follows;
◆ The thickness of residual castable at the bottom of the furnace was measured to be 550mm, the original thickness was 800mm, and the erosion was 250mm.
◆ Above the slag door, the residual thickness of the side wall castable ranges from 200mm to 300mm, and the original thickness is 350mm.
◆ The residual thickness of the castable in the elephant foot area is 550mm, and the original thickness is 700mm.
◆ From this, the erosion diagram of blast furnace castable is reduced, as shown below, and the sky blue line is erosion.
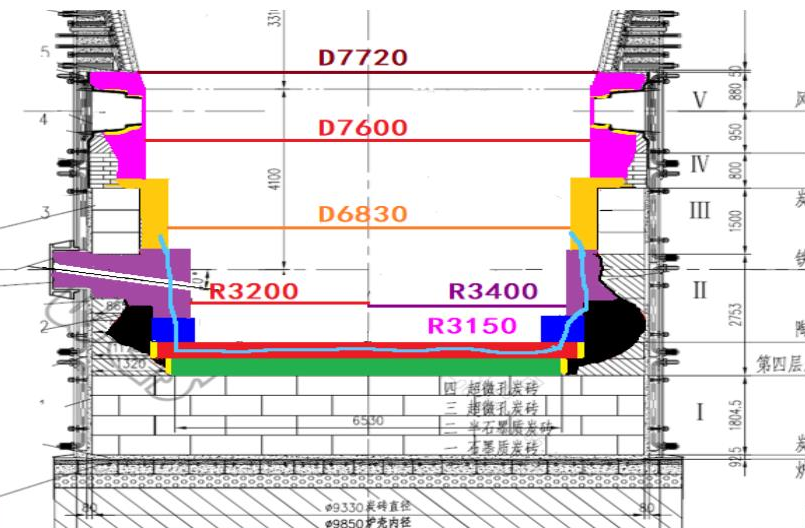
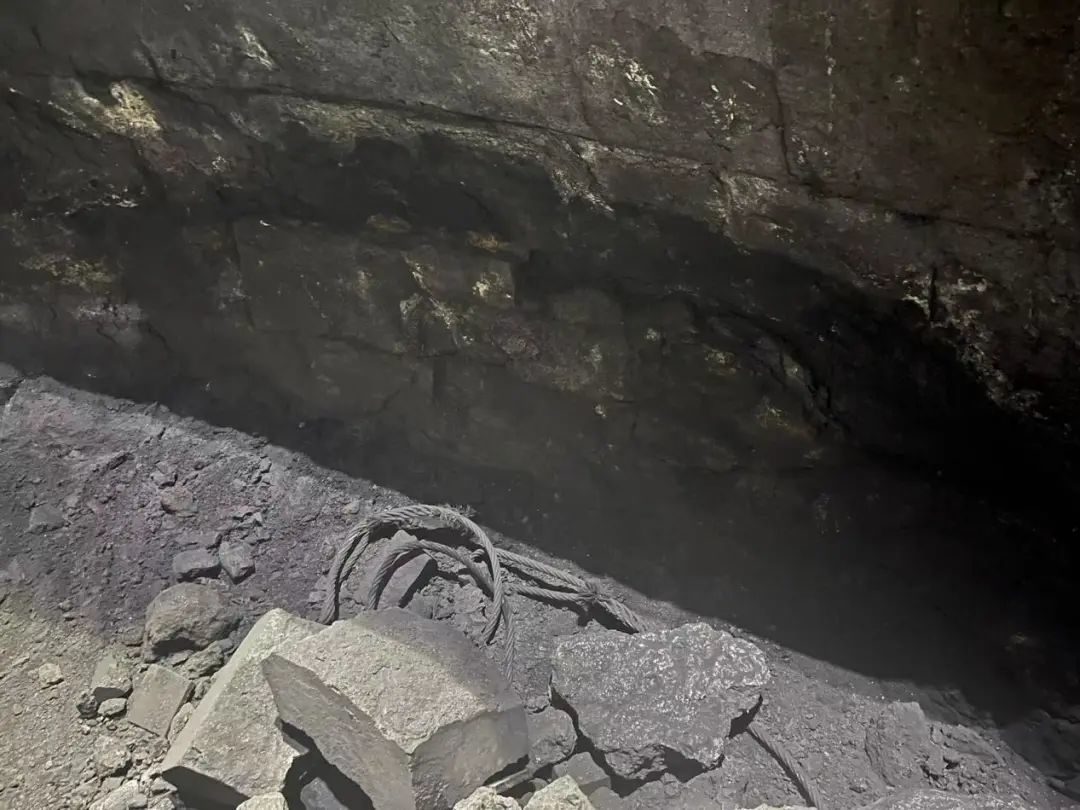
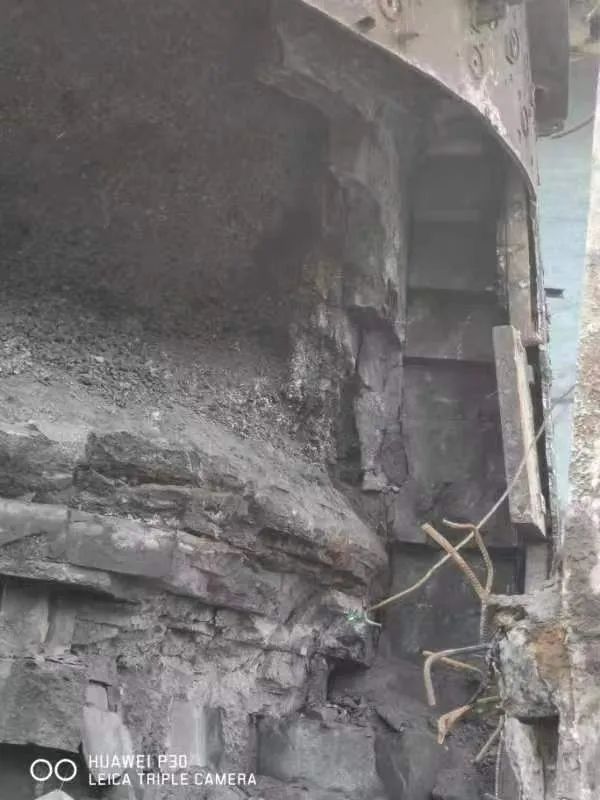
6. Summary
1, blast furnace body safety is the primary task of all blast furnace operation managers, to combine the raw material situation, the degree of production enhancement to choose a reasonable cooling system and air supply system, and finally form a reasonable erosion state.
2. The furnace protection work in the later stage of blast furnace is particularly important. More blast furnaces in Shagang adopt the early, small and long-term furnace protection methods to ensure the overall safety and control of the furnace body.
3. Whether the central airflow of the blast furnace is active is very important to the safety of the furnace body, and it is not recommended to develop the edge operation system easily.
4, Huaxi science and technology furnace cylinder overall pouring technology (patent number: ZL 201610353176.4) is a rapid repair of blast furnace furnace cylinder and ceramic cup way, has been widely recognized, the market share has reached 55.98 percent.
5, Shagang 4# blast furnace erosion state is more serious before the repair, local area has reached the warning temperature difference and heat flow level, fortunately, timely repair pouring. After 2 years and 4 months of use, the erosion state of the furnace bottom and furnace cylinder castable is generally good. If it is not removed, it is expected to be used for 3 to 4 years according to the current erosion state, exceeding the expected service life.
References: Shagang Group's "Analysis of Erosion State of 4# Blast Furnace Hearth of Shagang"